Printed from acutecaretesting.org
October 2014
POCT in emergency rooms: One key factor for process streamlining with Lean Management
METHODS
LEAN EMERGENCY MANAGEMENT IN THE PGS WITTENBERG
The Protestant hospital Paul Gerhardt Stift (PGS) in Wittenberg, located between Berlin and Leipzig, has 400 beds and belongs to a private hospital chain of the Paul Gerhardt Diakonie Group (PGD) with hospitals and special-care homes mainly in Berlin and its surroundings.With the main aims to reduce long waiting times for patients, to increase patient safety and to design a flexible organization structure [2] all over the hospital and already at check-in, the hospital management decided to start the initial Lean project in the ED.
Consequently, a project group consisting of employees of all careers, disciplines and hierarchies working in the ED was established. They received detailed training in Lean methods, such as value stream mapping (VSM), a Lean tool to compare current and future states of processes by focusing on waste drivers, mainly time.
Relevant process owners created the current-state map with the target to show the actual process and to analyze main problems. To illustrate the complexity and need for speedy diagnostics, the project group agreed on mapping patients with abdominal pain.
Another decisive factor for choosing this patient group is the comparatively high mortality of 5.1 % among these patients [3].
The following six process boxes were mapped (Fig. 1):
- administrative check-in
- primary case history taken by nursing staff
- diagnostics taken by nursing staff
- medical history taken by physician
- interdisciplinary consultation
- check-out
FIG. 1: VSM (current state) created to reflect the clinical process on patients with abdominal pain. Source: Own (project team work)
Already at this moment, the first correlations between problems and causes or waste drivers became obvious, since problems were analyzed by the project members in an open-minded, neutral atmosphere without blaming each other.
Then the project group prioritized and clustered the problems, subprocesses were mapped in individual meetings for a detailed analysis of the individual process boxes, and solution approaches were made step by step that were realized in test or pilot phases.
Time measurements were carried out to complete the current-state map (time level) and to distinguish value-creating activities from waste and non-value-adding activities. After successful testing plus some adjustments and final evaluation of the test results, standards were made.
RESULTS
Out of a variety of problem areas, the main waste drivers to be focused on were:
- bottle-neck already at check-in due to first-in first-out treatment
- not medically skilled staff defines further pathway
- nursing staff decides on diagnosis and even therapies
- double burden for physicians (on-call duty)
- missing availability of laboratory parameters and SOPs
INTRODUCTION OF A TRIAGE SYSTEM
Complex problems asked for complex solutions. Thus, the Manchester Triage System was introduced. Intuitive nursing experience yielded a structured instrument to assess patients’ needs for treatment, considering individual pains and complaints by using a validated system.
Besides quality control (especially risk management) and the option to initiate the treatment process, it is now possible to legally delegate medical activities to the assisting personnel [4].
INTRODUCTION OF POCT
The problematic transport of blood samples to the laboratory called for a more precise analysis. In fact, measurements showed that it already took 37 minutes to carry blood samples from the ER to the laboratory, whereas the first laboratory results were available after 71 minutes (average).With the POCT equipment and the combination of laboratory and performance standards, physicians are now so fortunate to receive relevant data after 2 minutes for blood gas analysis (especially electrolytes, hemoglobin and metabolic parameters) and important data from the immunoassay devices after 15-20 minutes.
This means an immense improvement of patient safety and staff satisfaction. These standards have been integrated in the order-entry system of the hospital and serve as general guidelines for the whole organization.
The purchase of the two analyzers was suggested on both medical and process grounds.
ARGUMENTATION FROM A MEDICAL POINT OF VIEW
Two main aspects have to be considered: First of all, the increase of medical quality and secondly, the improvement of medical effectiveness for acute patients (rule-out) [5].
The justified arguments follow increased medical-logistic demands in diagnostics and therapy of patients with highly acute or even life-threatening diseases.
Here, one must consider both demands resulting from modern medical expertise as well as SOPs in combination with optimized and efficient patient paths plus proximity conditions and processes that also focus on relatives’ requirements.
The blood gas device provides important acute parameters that play a decisive role in emergency medicine, since precise and valid results are available in time and on spot. Loop ways and external influences are omitted.
ARGUMENTATION FROM A PROCESS POINT OF VIEW
To increase process stability and quality, the project group made the following future-state map, consisting of six process boxes:
- administrative check-in
- initial assessment by nurse (Manchester Triage) in combination with diagnostics (POCT) according to standards (new SOPs)
- medical diagnostics or waiting area 1 or 2
- medical consultation/indication
- check-out
The new patient path of the ER is illustrated in Fig. 2:
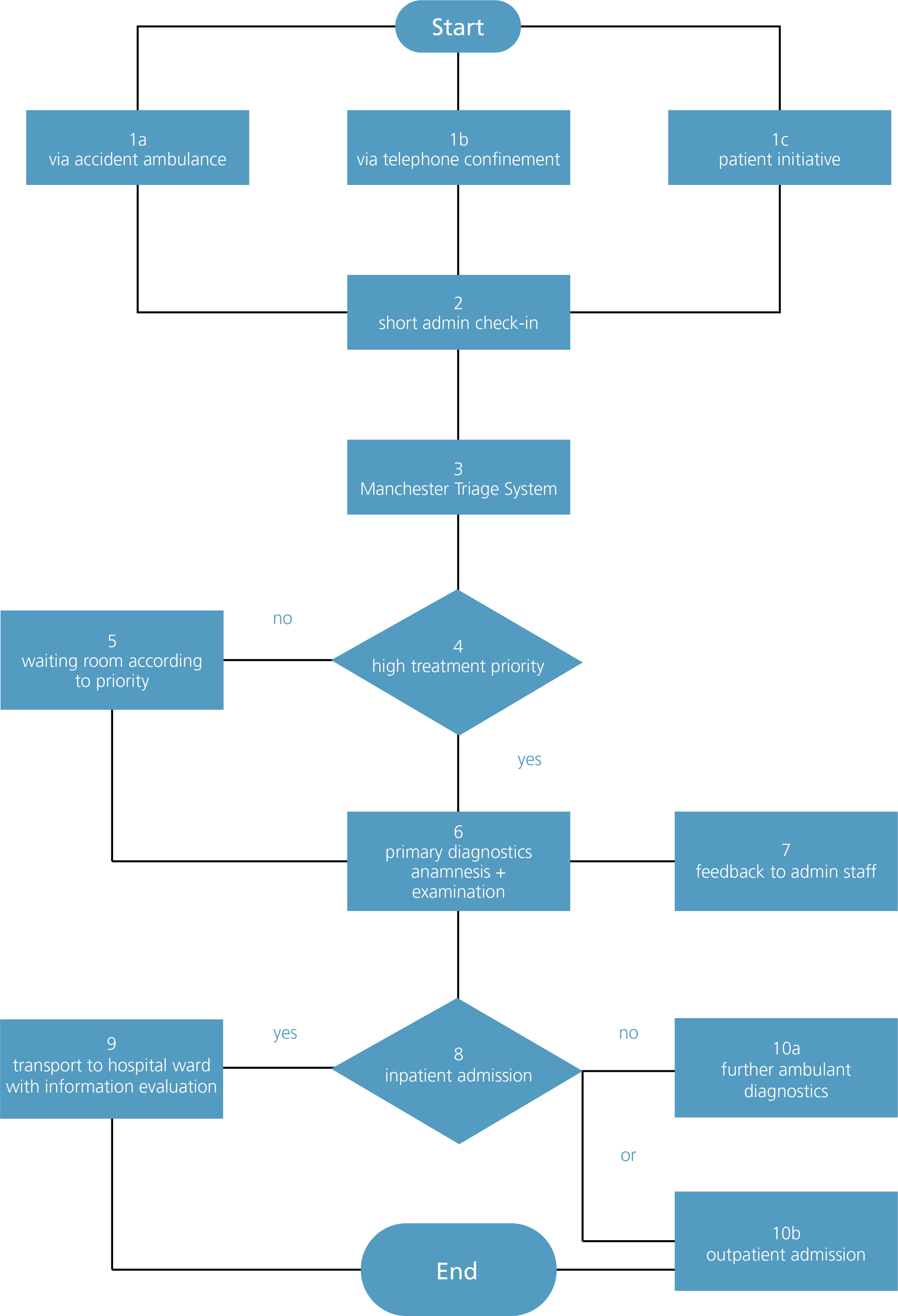
FIG. 2: New patient path with integrated Manchester Triage. Source: Own
Still, patients check in at the administration area but are then transferred immediately to the triage room. The nurse in charge determines the treatment priority according to the standardized presentation charts, examines vital signs and decides on taking laboratory parameters at the POCT equipment according to the laboratory standards.
LABORATORY AND PERFORMANCE STANDARDS
- Profile A – Chest pain/dyspnea
- Profile B – Abdominal pain, incl. gastrointestinal hemorrhage
- Profile C – Pneumonia/sepsis
- Profile D – Apoplexy/neurological deficit
- Profile E – Preoperation
- Profile F – Polytrauma
All profiles include laboratory standards, vital signs and medical orders. Due to that, variances are reduced and errors are minimized, physicians on duty receive credible diagnoses in a shorter time (no symptom-based estimated diagnosis anymore) and postprocesses such as consultations, indications and continuing therapies are accelerated.
Due to the use of POCT devices, opportunity costs caused by waiting times, transport and interruptions of workflow could be decreased or eliminated.
EVALUATION
Evaluation of the key data started in the 3rd quarter of 2012 and was performed throughout the year 2013 (December 2013 excluded, since it was not representative).
Following, the results of a total of 406 MTS forms for patients with abdominal pain showing up in the ED in 2013 are displayed in Figs. 3 and 4.
FIG. 3: Graphic charts showing rated patients according to MTS priorities. Source: Own (406 protocols)
FIG. 4: Graphic chart showing total length of stay of patients. Source: Own (406 protocols)
Due to the opening of a Cardiology Department with an integrated Catheter Laboratory in the beginning of 2013, the hospital had additionally to cope with an increasing number of patients with cardiac diseases.
Since especially these acute patients benefit from the triage system, evaluation of 538 MTS forms for this patient group was performed in 2013 also. Results are shown in the following Figs. 5 and 6.
FIG. 5: Graphic chart showing rated patients according to MTS priorities. Source: Own (538 protocols)
FIG. 6: Graphic chart showing total length of stay of patients. Source: Own (538 protocols)
As one can see, the ED is still suffering from crowding effects after physician’s consultation due to long waiting times for interdisciplinary consultations and unsatisfactory bed-allocation management.
Therefore, only a slight decline in the average total length of stay could be observed.
Most significant is the analysis of the patient flow within the first four process steps (admission to first view).
Within these process steps, the length of stay for patients with abdominal pain decreased from an average of 60 minutes to less than 21 minutes (3rd quarter of 2013), tantamount to a 65 % decrease of LOS in this period.
Cardiac disease patients’ first view is in average less than 9 minutes in the same quarter and can be doubtlessly regarded as excellence in patient safety.
2013 | Abdominal pain | Cardiac disease | |
Month | min | min | |
January | 30.33 | 12.39 | |
February | 37.04 | 19.46 | |
March | 23.32 | 16.17 | |
1st quarter | 32.23 | 16.01 | |
April | 35.55 | 21.05 | |
May | 19.50 | 20.16 | |
June | 16.37 | 21.03 | |
2nd quarter | 24.26 | 20.75 | |
July | 19.48 | 9.46 | |
August | 15.57 | 9.10 | |
September | 26.55 | 7.16 | |
3rd quarter | 20.53 | 8.57 |
TABLE II: Waiting time of representative patient groups from admission to first view 2013. Source: Own
Decision making for diagnostic findings and therapy is speeded up due to just-in-time laboratory values.
With POCT equipment, turnaround times for blood tests could be decreased significantly (BGA from 44 to 2 minutes and troponin from 91 to 14 minutes in average).
Waiting time | 2011 Laboratory | 2013 POCT |
min | ||
BGA | 44 | 2 |
CRP | 82 | 16 |
Troponin | 81 | 14 |
D-dimer | 58 | 12 |
TABLE III: Comparison of waiting times for TAT of certain blood samples analyzed in laboratory vs. POCT. Source: Own
DISCUSSION
POCT equipment plays a key role in realizing holistic solution concepts for streamlining processes, and modern emergency departments are not imaginable without them anymore.
The combination of
- a triage system
- strategic operating standards
- symptom-based laboratory standards
- medical equipment
- a staff quality mix
allows
- the decrease of turnaround times and lengths of stay
- the reduction of process costs (especially opportunity costs)
- intelligent control of patient flow (avoidance of crowding effects)
- increase of patient safety (risk prevention)
- improved employee satisfaction
Due to the initial information about treatment priority given by the triage nurse combined with first vital signs and parameters from the POCT devices according to the standards, one can now consider a reorganization of the previously inflexible processes dominated by the organization into streamlined process working conditions that result in patient safety and employee satisfaction.
Future work will deal with the last two process boxes (consultation and check-out) since the hospital is still struggling with bottle-neck problems at the end of the process chain that negatively influence the total value stream.
Already, the patient transport team service and bed-capacity management have been optimized to relieve the ED, and a Decision Unit for patients that ought to be monitored for decision making (check-out or ward) has been operating successfully.
CONCLUSION
Lean Management tools provide the opportunity to build more effective and safer clinical processes in the ED.References+ View more
- Moskop JC, Sklar DP, Geiderman JM et al. Emergency department crowding, part 1 – concept, causes, and moral consequences. Ann Emerg Med 2009; 53, 5: 605-11.
- Mackway-Jones K, Marsden J, Windle J. Ersteinschätzung in der Notaufnahme. Das Manchester Triage System. Bern: Verlag Hans Huber, 2011.
- Möckel M et al. Chief complaints in medical emergencies: do they relate to unterlying disease and outcome? The Charité Emergency Study (CHARITEM). Eur J Emerg Med 2013, 20: 103.
- Paul Gerhardt Diakonie. Ausgezeichnete Behandlungsqualität. http://www.pgdiakonie.de/waldkrankenhaus/ueber-uns/qualitaetsmanagement-lean-management/. 2012
- Petrausch S. Interview vom 1.9.2011. Paul Gerhard Stift Lutherstadt Wittenberg.
References
- Moskop JC, Sklar DP, Geiderman JM et al. Emergency department crowding, part 1 – concept, causes, and moral consequences. Ann Emerg Med 2009; 53, 5: 605-11.
- Mackway-Jones K, Marsden J, Windle J. Ersteinschätzung in der Notaufnahme. Das Manchester Triage System. Bern: Verlag Hans Huber, 2011.
- Möckel M et al. Chief complaints in medical emergencies: do they relate to unterlying disease and outcome? The Charité Emergency Study (CHARITEM). Eur J Emerg Med 2013, 20: 103.
- Paul Gerhardt Diakonie. Ausgezeichnete Behandlungsqualität. http://www.pgdiakonie.de/waldkrankenhaus/ueber-uns/qualitaetsmanagement-lean-management/. 2012
- Petrausch S. Interview vom 1.9.2011. Paul Gerhard Stift Lutherstadt Wittenberg.
May contain information that is not supported by performance and intended use claims of Radiometer's products. See also Legal info.
Acute care testing handbook
Get the acute care testing handbook
Your practical guide to critical parameters in acute care testing.
Download nowScientific webinars
Check out the list of webinars
Radiometer and acutecaretesting.org present free educational webinars on topics surrounding acute care testing presented by international experts.
Go to webinarsRelated webinar
The Impact of POC Testing on the Quality and Efficiency of Patient Care in the Emergency Department
presented by Tim Harris, MD, Prof.
Watch the webinar